Control Strategies for Optimal Performance: The Driving Power Behind Brushless Motors
- Manu Agarwal
- Jun 2, 2023
- 5 min read

Brushless permanent magnet motors are electronically commutated and require a control system to control the key motor parameters like torque, speed and position. The performance of the motor in terms of efficiency, noise and torque ripples etc will depend not only on the design and construction of the motor but also on the control system strategy which would vary in terms of hardware and software complexity to optimise the motor performance depending upon its application
Brushless permanent magnet motors are being increasingly adopted in different applications like electric vehicles, robotics, HVAC systems, industrial automation, consumer appliances etc. due to their higher efficiency, reliability, and low maintenance requirements. Brushless motors are electronically commutated thus enabling for more efficient operation over mechanical commutation and a significantly higher optimized performance due to the different control strategies.
In this article we will explore the core operating principles of a brushless motor and discuss its control system i.e. the brain behind the motor and the different strategies which can be implemented to achieve optimal motor performance.
Operating Principle
The operating principle of a brushless motor involves the interaction between the rotating magnetic field created by an electromagnet i.e. the copper windings in the stator and the constant magnetic field created by the permanent magnets i.e. the rotor to produce torque. The rotating magnetic fields are generated by providing electric current to the stator windings in a particular sequence depending upon the rotor position or other feedback from the motor. This pattern of current excitation is generated and provided by an electronic motor controller and hence brushless motors are electronically commutated and have different control strategies.
Motor Control System
The motor control system as the name suggests primarily should be able to control the torque of the motor directly. But direct torque control is very expensive due to the high cost of torque sensors. Considering that typically torque is directly proportional to the current, torque can thus be controlled by using a current control, which is also important for speed or position control of a motor.
The two basic types of control systems are open-loop control and closed-loop control. In more advanced motors controls a feed forward control is also used along with the feedback control.
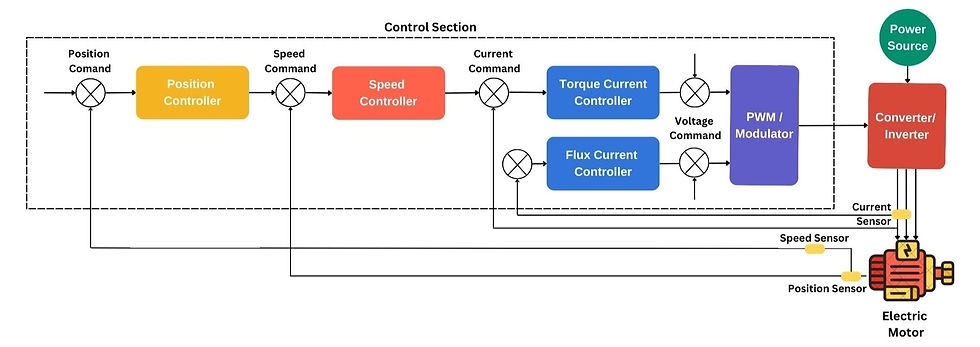
Figure 1: Motor Control System Block Diagram
Figure 1 above gives an overall configuration of a motor control system. It can be observed the following key sections make up the control system for the electric motor
Controller: Proportional-Integral (PI) controllers for widely used for controlling the position, speed and current in a motor.
Power Converter: Bridge rectifiers or a PWM inverter is used to provide a trapezoidal or a sinusoidal input voltage waveform.
Sensors: Devices which measure the output parameters like current, speed or position and are used to provide the feedback in a closed loop system. They are typically hall sensors, encoders or current sense resistors.
Different combinations in this control block and using different control algorithms for PWM generation for the converters leads to different commutation strategies, each of which has several advantages and disadvantages in terms of the motor performance and cost. Control systems can thus range in computational complexity, processing power requirement and size among other factors.
The simplest one like an open loop control system for a BLDC motor which has no information about the rotor position or current could be extremely cost effective but highly unstable thus poorly performing. A complex closed loop vector control system with a pure sinusoidal inverter using space vector PWM with Third Harmonic Injection, for a PMSM would give the highest dynamic performance with the lowest noise and torque ripples but on the downside would be quite expensive.
Thus depending upon the requirements and the operating conditions the brushless motors performance can be optimised by selecting the appropriate control strategy.
Typical Control Strategies
Brushless motors can have either a sinusoidal or a trapezoidal back emf waveform depending upon the motor construction (Refer our blog article on the differences between a PMSM and a BLDC motor). For the most efficient operation a trapezoidal back emf motor should be driven by a trapezoidal control strategy while a sinusoidal back emf motor should be driven by sinusoidal commutation. They can be interchanged as well but it will result in lower average torques and higher torque ripples.
Control systems can be categorised in broadly the following four types.
Open Loop vs Closed Loop: Open loop control systems will lead to unstable performance and the brushless motors could very easily go out of synchronism. Without the permanent magnet rotor position, detailed and complicated motor models need to be developed for a stable open loop control system.
Trapezoidal vs Sinusoidal Commutation: Trapezoidal control systems (like the 6 step commutation) are easier to implement and require lower processing power than sinusoidal controls (like Sine PWM, Third Harmonic Injection or Space Vector PWM) but on the downside have higher torque ripples and noise levels. This is fundamentally due to trapezoidal commutation having higher low-order harmonic distortions or the total harmonic distortion (THD).
Vector vs Scalar: Vector control (like Field Oriented Control or Direct Torque Control) enables independent control of torque and speed by its ability to decouple and control the two orthogonal components of current (Torque Current and Flux Current) visualised as a space vector having a magnitude and an angle. Scalar control (like Voltage/Frequency ratio) is able to control only the magnitude and the frequency of the supply voltage without control over the phase.
Sensored vs Sensorless: Rotor Position can be established either through use of sensors like resolvers, hall-effect sensors and encoders or through a sensorless approach where the back electromotive force (back EMF) magnitude and polarity indicates the rotor position. Sensored control has the advantage of being precise and motor performance will be high at even low speeds compared to a sensorless approach. Sensorless control increases the reliability while also increasing the computational complexity of the control system.
Different control algorithms can be devised by choosing from the different control systems. For example a complex algorithm will be needed for a closed loop, sinusoidal, vector control with an encoder. Like in servo drives.
A Quick Comparison
A brief comparative analysis is done for the four most common types of control strategies and tabulated according to performance (efficiency, noise and torque ripples), software & hardware complexity, cost and applications where they can be used. All of these strategies can have a sensored or a sensorless control approach.

Figure 2: A Brief Comparison of the Most Common Type of Control Strategies
It can be stated that the Field Oriented Control (FOC) is the most versatile in terms of torque, speed or position control delivering the highest motor performance but has the disadvantage of high complexity and cost.
Conclusion
The operating principle of a BLDC motor involves the interaction between the stator and the rotor, controlled by an electronic controller. There are several strategies for optimizing the performance of brushless permanent magnet motors with each having its own set of advantages and disadvantages, and the best strategy for optimizing performance will depend on the specific application. By implementing effective operating principles, engineers and designers can ensure that BLDC motors operate at their maximum potential, resulting in increased efficiency, reliability, and lifespan.
Alphasine Technologies is a technology start-up designing and manufacturing energy-efficient permanent magnet brushless motors and their controllers in Lucknow, India. It is our vision to be a global leader in the space of ultra-high efficiency motors, drives and controllers providing cutting-edge technology to numerous industries like electric mobility, aerospace & defence, industrial automation, robotics and consumer appliances.
In the next article we will further explore control strategies and focus on the different power converters used in the commutation of brushless motors.
Really liked the content on the blog !! If you are interested in checking out my website, I have attached the link below URL: https://mechtex.com/bldc-motors Do like and comment :)